Mechanical
The mechanical system of the game.
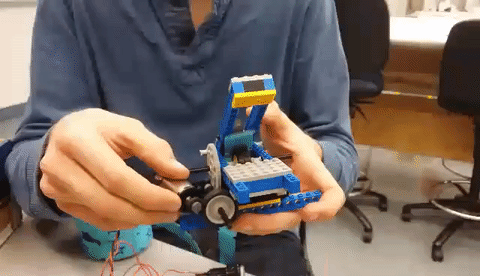
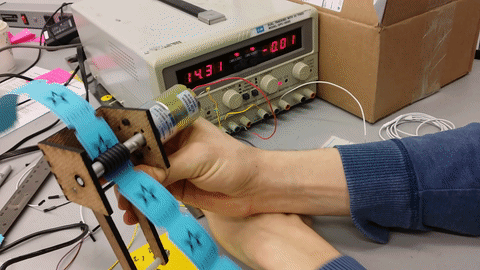
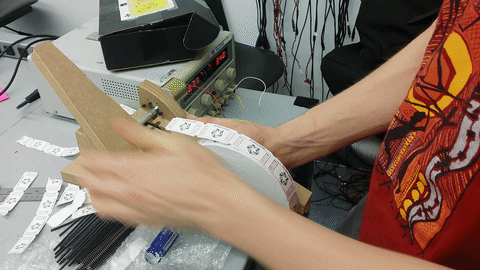
Our current mechanical assembly is broken into two parts: the enclosure and the ticket dispenser.
The enclosure
The enclosure was CNC routed out of ¾” MDF to get precise mitered edges that mate perfectly. On the opposite, angled faces 16 holes were drilled to accommodate the button-light arrays. The ergonomics of the angle of these sides was influenced by playtesting and the v-bits we had at our disposal. Unfortunately, I didn't predict all the hole operations needed on each face of the enclosure, so a tasteful amount of handrouting and jig sawing was needed to accommodate elements like the rear door and the coin mech. The exterior received three coats of spray paint to get the crisp black, box-arcade aesthetic and the instructional text was vinyl cut.
The ticket dispenser
We knew that this game would spit out loads of tickets, so being able to gracefully change out spools was an important consideration. Knowing that there might come a day when we aren't the ones changing out the reels, we tried to create a dispenser that was as intuitive to interact with as possible. We went through three major iterations:
- 1. Just making sure that we could grip the tickets tightly enough to resist the forces of people ripping them off. This assembly consisted of two rods sheathed in o-rings pressed together.
- 2. Once we worked out the force of roller pinching and therefore the spring parameters and lever dimensions, we scaled up to an assembly that could also accommodate the reel of tickets. This first ticket holder utilized a magnetic rod that passed through the middle of the ticket spool which could easily be pulled out to allow for quick replacement of tickets. The problem with this configuration was the fact that magnets are super counterintuitive (how do they even work?) and so this design wasn't terribly intuitive. Another drawback was that the tickets weren't appropriately guided and so they were prone to falling off of their reel. This issue was exacerbated by the fact that the tickets would continue to spin on their rod even after the motor had stopped trying to feed them through the mechanism (thanks inertia!).
- 3. The last iteration we have created solves many of the problems of previous versions. The slippery steel rod was replaced by a shopbotted MDF tab to provide the needed tensioning resistance. To release the tickets, a restraining arm on a hinge was used because everyone knows what hinges look like and how they work.